概要
設備診断は、機械要素部品の劣化を定量化し破損前の適正なタイミングで交換することを目的としています。これに対して複合診断では、実際にはなぜシャフトに亀裂が入ったのかなど設備異常になった根本原因や製品の品質歩留低下の原因を複数の診断技術(振動・応力・潤滑分析・非破壊・3D計測等)を組合わせて究明し、改善案を提示します。
[複合診断の流れ]
お客様からのご相談を受け、現場下見・図面・設備の履歴・操業方法など調査し、診断計画を立案します。
計画後は、現地測定(現場一次所見)⇒解析⇒評価(原因の究明)を行い、原因に対してはお客様の諸事情に則した対策案を含めて
報告します。この中で特に診断計画の立案と解析原因究明は、多くの診断経験と技術が求められます。
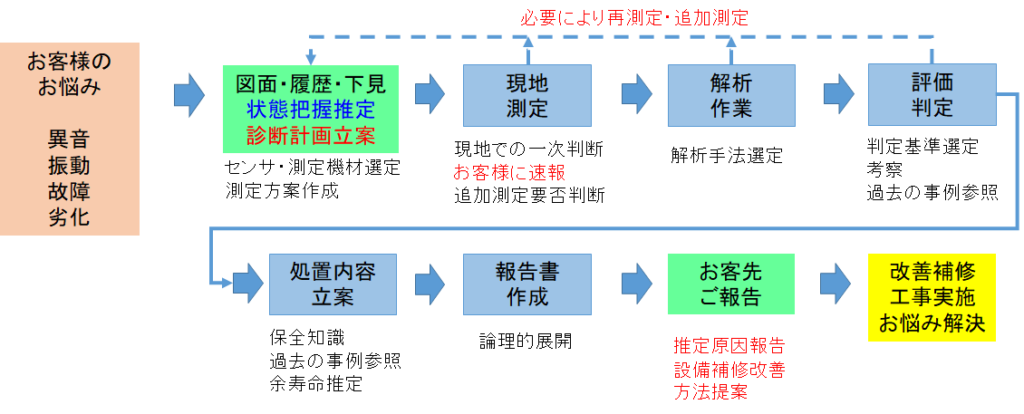
実績
- 油圧プレス機 シリンダーロッド折損原因究明
設備状態を評価することなく使用を継続されたためシリンダーの折損に至り、復旧まで1ケ月という致命的故障となりました。お客様から故障発生防止のための折損原因解明を依頼を受け複合診断を行いました。
①診断計画の立案
まずは設備の動きを想定し、定量化するために、診断計画を立案しました。
現場下見と図面考察および故障発生個所から、必要な測定箇所・項目・適性なセンサを選定します(このケースでは変位・応力・圧力など約10箇所を最終的に選定)。
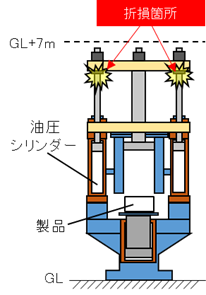
② 測定解析評価
設備の停止タイミングをお客様と調整のうえ、センサの仮設工事を行い稼働中のデータを収集します。収集した時系列データから設備の動き解析した結果、油圧シリンダーの内部リークによる左右の不同調動作により、ロッド固定部へ繰り返し負荷がかかることにより折損に至るメカニズムを解明します。
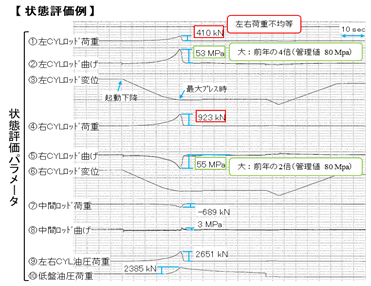
③ 結果報告と対策案提案
お客様には調査解析結果と根本的な原因をできるだけ分かりやすく報告します。
また、合わせて今後の効率的な設備の維持管理方法を対策として提案します。具体的には、定期診断を年1回実施し設備状態を監視するとともに、その結果を受けて整備を優先するプレス機を決定するという当社の提案を採用頂き、当社にプレス機の定期診断と整備をご依頼いただきお客様の安定操業の一端を担っています。
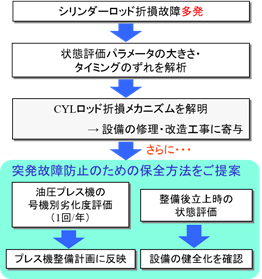